But I may have been a little overachieving.
I've got one of
these which I picked up off ebay about three years ago for only 200 pounds, in a non-working state. It was working perfectly about an hour after being unboxed (a freaking HUGE box,as well, it was absolutely enormous), as the fault was merely a cheap and underspecced 12v transformer in the power supply.
All I had to do to make it actually useful was take it completely to pieces, remachine all the mechanical parts in the XY mechanism so they fitted correctly and ran smoothly, rewire it to make it safe, rebuild it, remove all the drive electronics other than the EHT power supply and replace them with something useful, rewrite the firmware to drive the mechanism, and align it correctly. Oh yes, and machine up a new lens holder with an air feed, add said air feed, add an adjustable bed, and align
that. Easy.
It was about four days solid, but it was well worth it, as the thing works amazingly well and gets used several times a week. While it will only cut non-metallic things, there are a surprisingly large number of projects where either wood or acrylic are the right material for the job. It's an absolute godsend for model aircraft work, for example, and all my electronic prototypes end up in nice custom acrylic cases

But, after a while, of course, the old problem sets in.
It's not big enough.
It's not fast enough.
It won't cut thick enough material.
The usual complaints

So I designed and began building a bigger, faster, more powerful one. I may have become slightly carried away...
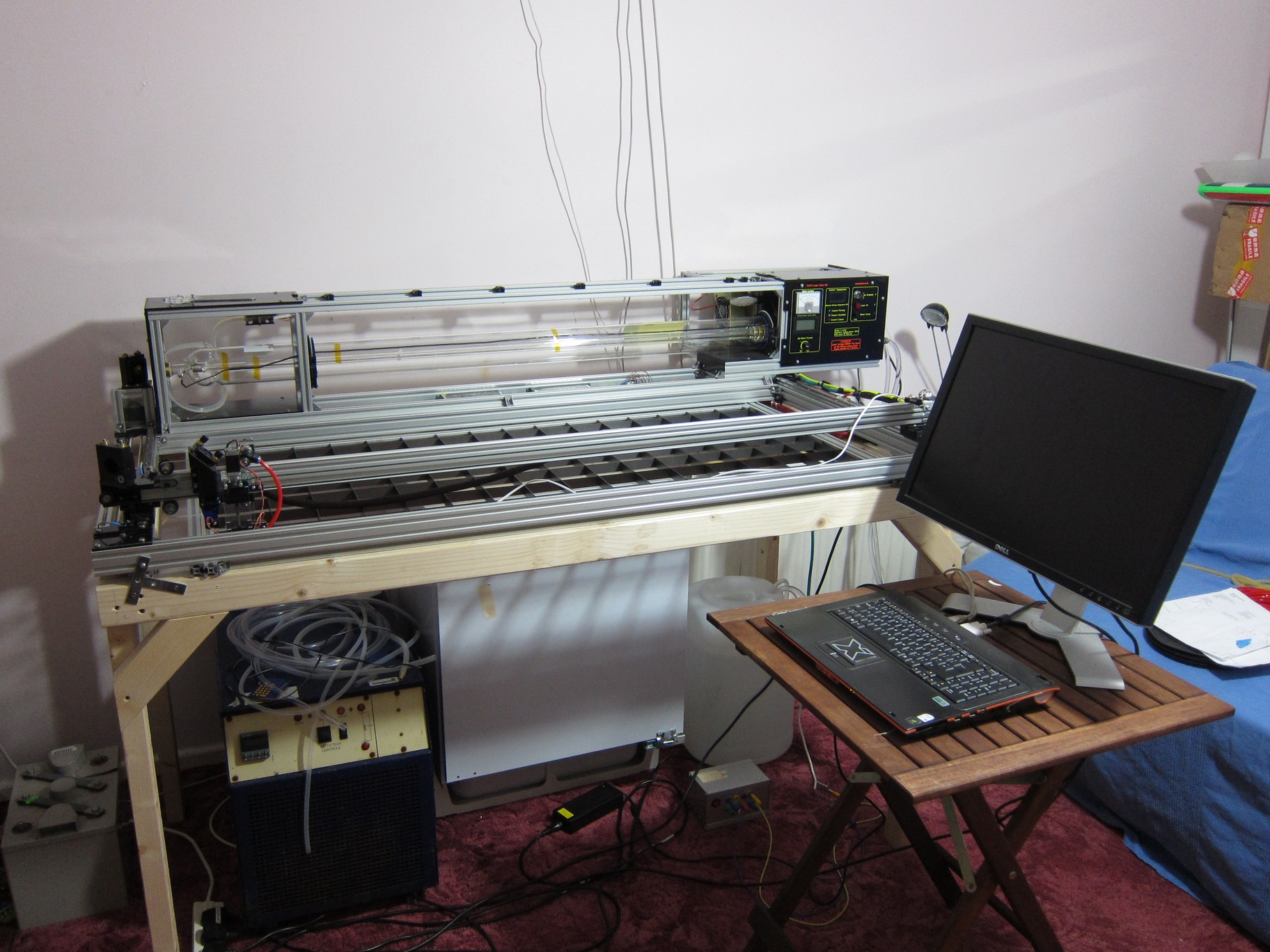
Now that it's nearly finished, I'm looking at it and thinking, "Ummm..."
I'm rather pleased, overall. It was designed in such a way that the grid bed can be removed so a standard 8 x 4 plywood sheet can be slid in and cut up in just under 600mm tall pieces. The cutting area is 1245x595mm which is pretty large, while it has a 100W CO2 laser tube in it, which is absolutely huge. The tube is 1.7 metres long!
I designed the entire thing in CAD, then had all the aluminium extrusion parts cut to order. Everything just bolted together in a very pleasingly accurate manner. Most of the fiddly bits are made out of 5mm acrylic, which is a surprisingly structural material as long as it's not bent too much. It doesn't like that.
Amusingly, laser cutters self-replicate. I made very extensive use of the small one to make the large one. Especially for things like very nice control panels.
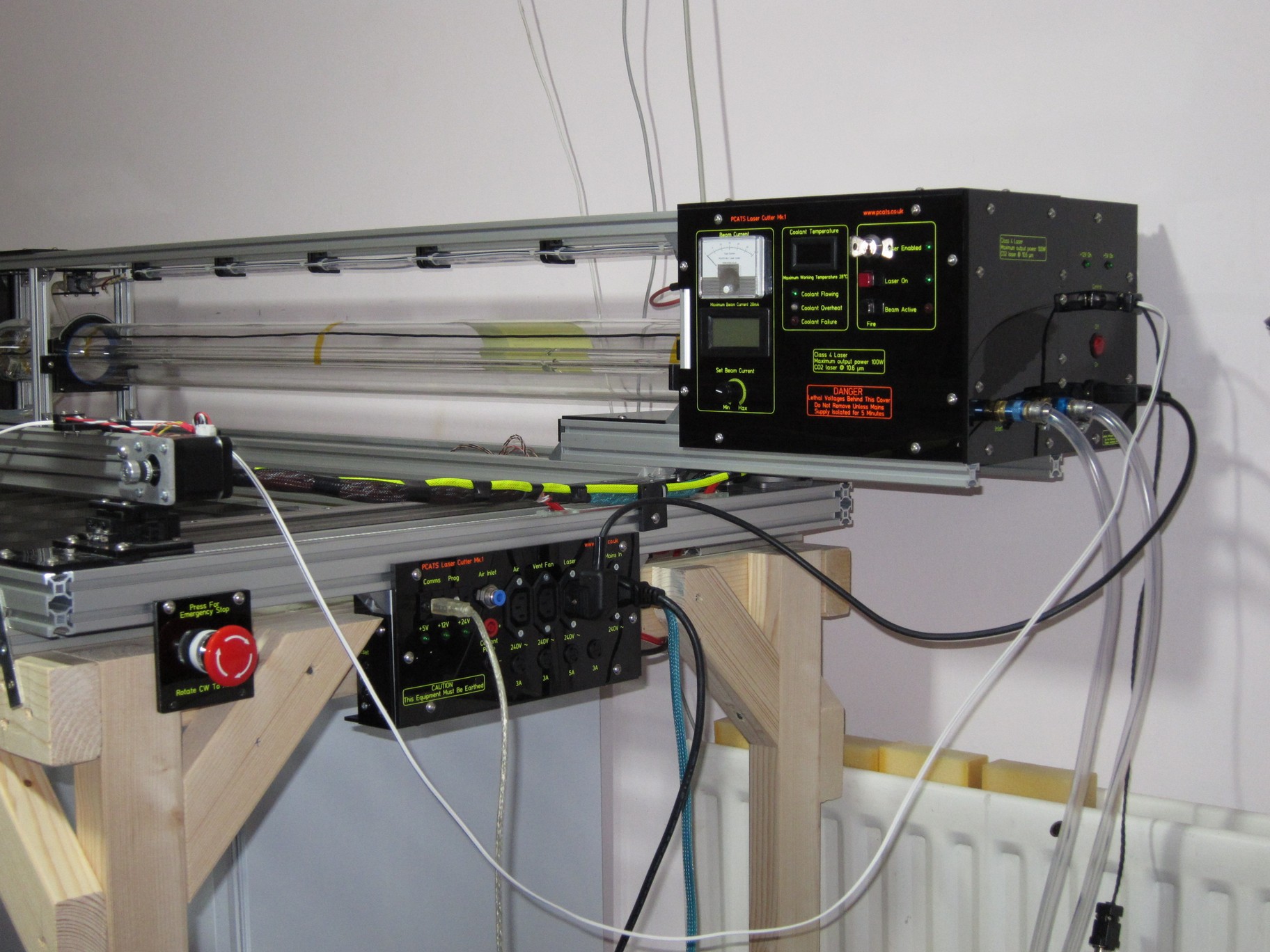
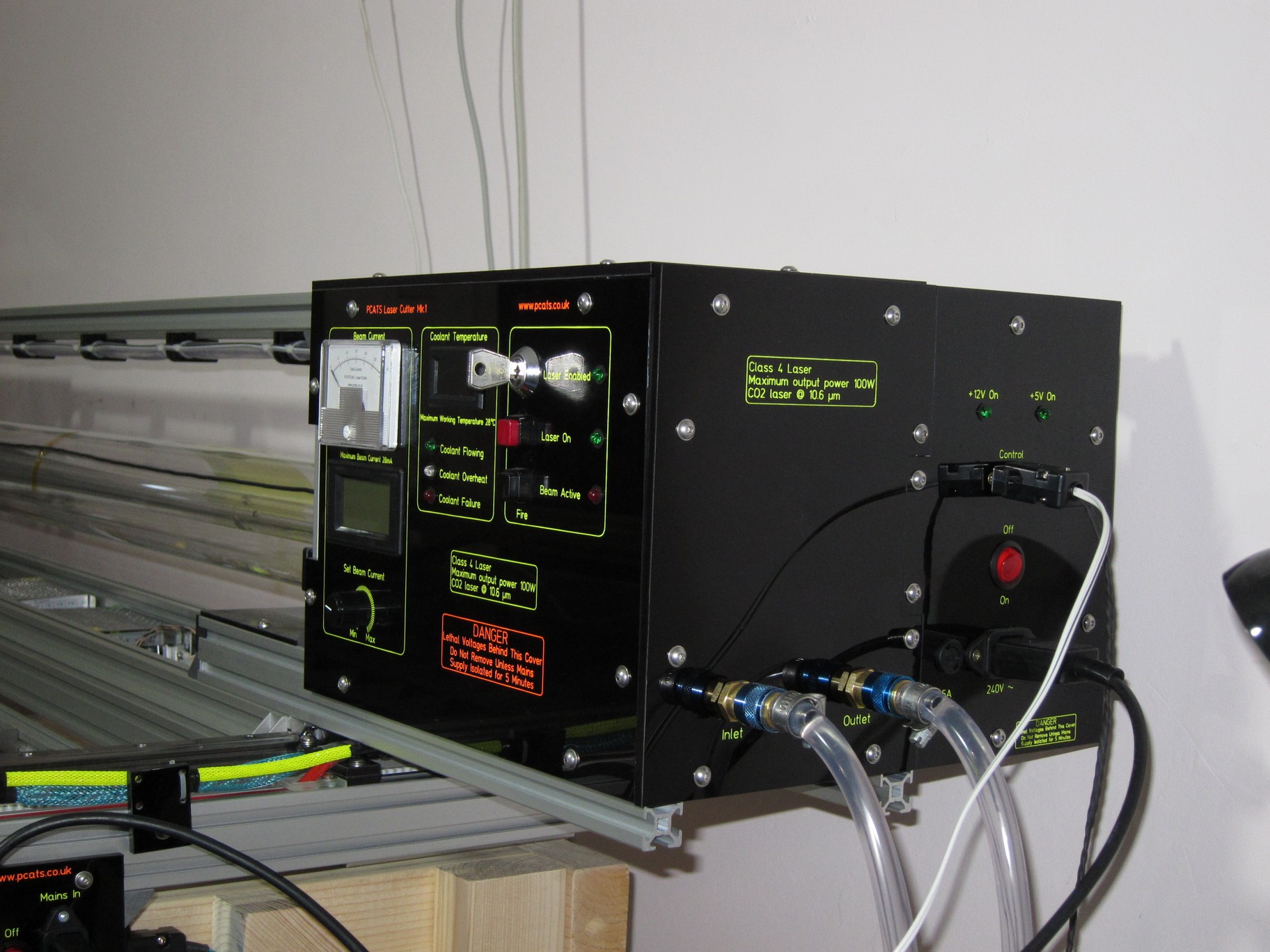
The laser is designed as a completely independent intelligent peripheral, the idea being I could fit a smaller one if necessary. In fact, I designed it around a 50W tube but the 100W one came up at a silly price during the later assembly stages and I couldn't avoid buying it

It did increase the cost of the project, as I then had to design a new housing for it, and get new mirrors and a power supply as well, but I think it was worth it. I can always sell the 50W one again.
It's entirely my own design, to meet a specific requirement, but I will admit that seeing it fully assembled it's slightly larger than I pictured...
On the other hand, it works, it's cost less than 20% of how much a really cheap commercial one that size would, and I've added a lot of things I wanted that I haven't seen on other ones. Plus it was a lot of fun building it. Now I have to figure out where it will live, I need my living room back!
pca